Plastic extrusion for creating standardized, top-grade parts
Plastic extrusion for creating standardized, top-grade parts
Blog Article
Key Advantages and Considerations of Implementing Plastic Extrusion in Your Projects

Comprehending the Fundamentals of Plastic Extrusion
Plastic extrusion, a staple in the production sector, is a process that entails melting raw plastic product and improving it right into a continual profile. This profile, as soon as cooled, can be reduced right into wanted sizes or curled for later use. The appeal of plastic extrusion lies in its flexibility. A wide variety of items, from piping to home window structures, can be created. The process needs an extruder, a complex maker with a warmed barrel, a turning screw, and a die at the end. The plastic product, in the type of pellets, is fed right into the extruder, where it's melted and forced with the die, taking its shape. The option of plastic and the style of the die figure out the item's attributes.

The Economic Advantage of Plastic Extrusion
The financial benefit of plastic extrusion lies mainly in 2 locations: affordable product manufacturing and beneficial manufacturing rates. With plastic extrusion, services can generate high volumes of product at a lower expense contrasted to other methods. Additionally, the process boasts a remarkable manufacturing speed, substantially lowering time and further enhancing its economic viability.
Affordable Product Manufacturing
A substantial advantage of plastic extrusion is its amazing cost-effectiveness. This manufacturing procedure allows for continuous, high-volume production with minimal waste, which equates right into lower costs. The raw products used, typically plastic pellets, are fairly economical contrasted to other compounds (plastic extrusion). The procedure itself needs less power than several various other manufacturing approaches, additionally lowering expenses. Furthermore, the extrusion procedure enables a high level of precision fit the plastic, minimizing the need for costly post-production modifications or corrections. The durability and long life of extruded plastic products usually indicate much less require for replacements, adding to long-lasting financial savings. All these aspects make plastic extrusion an extremely affordable option for lots of tasks, offering an attractive equilibrium in between expense and performance.
Beneficial Production Speeds
While maintaining the cost-effectiveness of the products, one more notable benefit of plastic extrusion exists in its fast manufacturing rates. This mix of high quality, rate, and cost-effectiveness highlights the considerable financial advantage of implementing plastic extrusion in different projects.
Versatility and Customization: The Toughness of Plastic Extrusion
One of the prominent site here toughness of plastic extrusion depends on its adaptability and personalization capacity. These high qualities open the door to unlimited design possibilities, giving manufacturers the ability to tailor items to details webpage requirements. This heightened degree of customization not only boosts product capability however likewise considerably improves item uniqueness.
Unrestricted Design Opportunities
Plastic extrusion radiates in its capability to use virtually infinite style opportunities. This approach provides freedom to create intricate shapes and intricate profiles, a feat difficult to achieve with various other manufacture techniques. Owing to the liquid nature of liquified plastic, the procedure is adaptable sufficient to generate a diverse array of sizes, types, and dimensions. The plastic can be adjusted to match unique specs, allowing for the manufacturing of tailored geometries and conference details client needs. Plastic extrusion can handle a selection of plastic types, expanding its application extent. This adaptable strategy, as a result, serves a large range of industries from building and construction to automobile, product packaging to electronics, and beyond. With plastic extrusion, the style possibilities are essentially limitless.
Enhancing Product Uniqueness
The flexibility of plastic extrusion can considerably improve item individuality. This process permits developers to trying out various forms, dimensions, and shades, providing them the liberty to develop unique items that stick out on the market. It is this personalization that provides a distinct identification to each product, differentiating it from its rivals.
In addition to its aesthetic benefits, the customizability of plastic extrusion additionally uses useful benefits. Thus, plastic extrusion not just increases item individuality yet additionally its energy and marketability.
Design Limitations in Plastic Extrusion: What You Required to Know
Just how can develop limitations potentially influence the process of plastic extrusion? While plastic extrusion is functional, style limitations can cut its benefits. Recognizing these navigate to this site restraints is vital for efficient implementation of plastic extrusion in your jobs.
Examining the Environmental Impact of Plastic Extrusion
While understanding layout restrictions is a considerable element of plastic extrusion, it is similarly crucial to consider its environmental implications. The process of plastic extrusion involves melting plastic products, potentially launching damaging gases right into the environment. Making use of recycled plastic materials in the extrusion procedure can lower environmental impact.
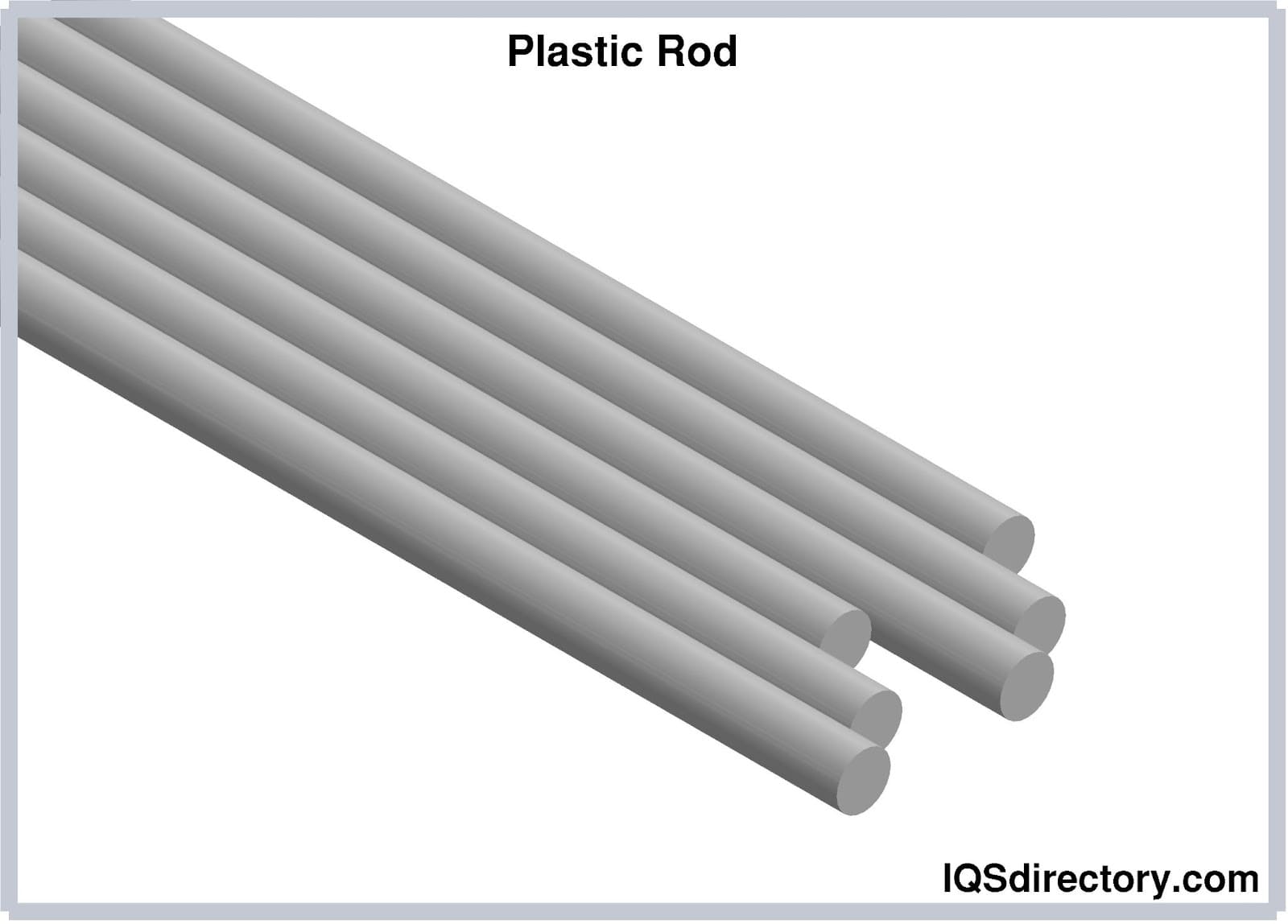
Case Research: Effective Projects Utilizing Plastic Extrusion
Success stories in the area of plastic extrusion are plentiful, demonstrating both the flexibility and performance of this production procedure. plastic extrusion. An additional effective instance is the manufacturing of plastic film for product packaging and farming. These circumstances show plastic extrusion's crucial duty in various industries, confirming to its flexibility, cost-effectiveness, and dependable result.
Final thought
Finally, plastic extrusion uses a cost-effective and effective technique for producing complex shapes with minimal waste. While it provides many advantages such as cost-effectiveness and flexibility, it's important to think about prospective design constraints and environmental effects. Implementing recycled or biodegradable products can mitigate these issues, enhancing sustainability. Integrating plastic extrusion into jobs can lead to effective end results, as evidenced by numerous study.
Plastic extrusion, a staple in the manufacturing industry, is a process that entails melting raw plastic product and improving it right into a continual account. Plastic extrusion can manage a variety of plastic types, broadening its application extent.How can make limitations potentially affect the procedure of plastic extrusion? The procedure of plastic extrusion entails melting plastic products, potentially releasing unsafe gases right into the environment. Making use of recycled plastic materials in the extrusion procedure can decrease environmental effect.
Report this page